Our engineers are always ready to listen to your ideas and concerns, and provide the solutions you need.
It all begins with the simple question: “How could this part perform better?”
Although Columbia Steel holds numerous patents, most of the innovative design takes place every day as engineers and field representatives work closely with end users to solve specific application problems. Incremental changes in design and optimum alloy selection often lead to significant improvements in the operation of equipment. Carefully studying the situation and identifying the problem or problems is key to developing improved wear parts that meet or exceed or customers’ needs.
Columbia engineers study the big picture and understand that any changes in processing equipment must take the entire operation into account. Our field representatives conduct reviews of customer plant design and equipment, material characteristics and performance records, as well as wear parts used. Our product engineers travel to study performance first hand. Recommendations can be as simple as selecting from Columbia’s large inventory of parts, or casting from our vast collection of patterns. Or a modification of an existing product may be in order: in the pattern design; in alloy and/or hardness levels; or by applying high-carbide overlays in our Xtend Process®. The result is replacement wear parts engineered to increase efficiency and reduce downtime.Check out just a few examples of innovative engineering that have considerably benefited our customers:
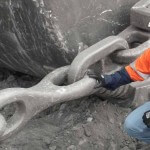

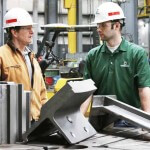
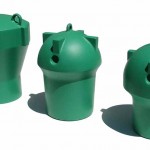